Usually, advanced printed circuit boards (PCBs) are known as High-Density Interconnector (HDI) boards that have a higher density of wiring. This means finer and denser lines followed by smaller vias. This particular field uses different techniques to achieve extreme miniaturization. In general, advanced PCBs are the types of boards that usually require different techniques, materials, and use cases. In our case, let us focus on the substrate material, which is used to build advanced PCBs.
Let us focus on PCBWay manufacturer, which offers a wide range of advanced PCB technologies.


Types of advanced PCBs
Besides the standard FR4, the most common types of advanced PCBs are:
- Flex
- Rigid-flex
- Aluminum
- Rogers
- Copper
Each of them has a specific purpose, and there should be a solid reason why you should select different type than FR4-based materials. Let us briefly look at each of them and point out the benefits of selecting one or another.
Rigid-Flex and flex PCBs
We have touched Flexible PCBs in a previous article (The Benefits of flexible PCBs). They are similar to standard PCBs except for the base material, which is based on flexible polymer (polyimide, PEEK, or conductive polyester film). The whole assembly may be designed as a single custom shape PCB which may conform the enclosure design and significantly reduce the amount of wire harness. According to PCBWay, flexible PCBs can have up to 8 layers with or without stiffening
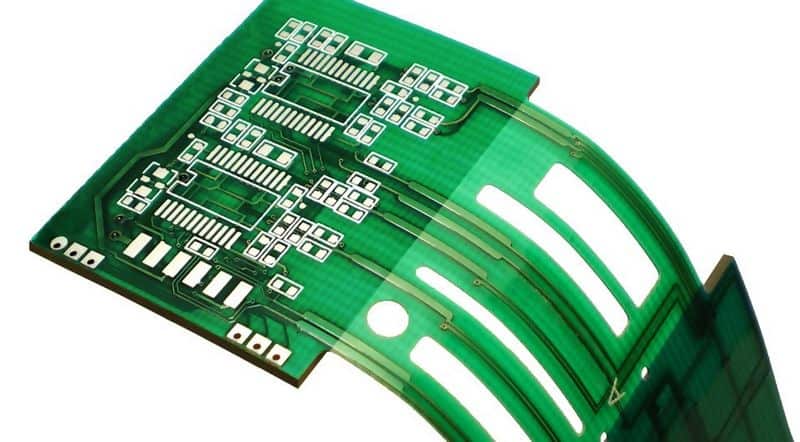
Flex-Rigid combines flexible and standard PCB that brings the best of both worlds. The designing and manufacturing process is more complex and may require additional skills to conform to differing design rules.
Aluminum PCBs
You have probably already seen an aluminum PCB on high-power LEDs and panels. As you may guess, aluminum plays a significant role in efficient heat dissipation.
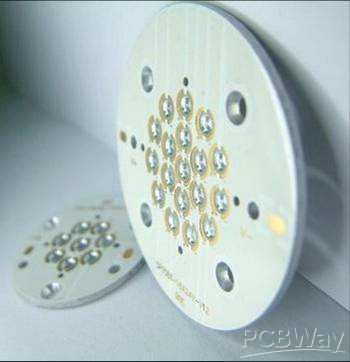
There are two types of aluminum PCBs:
- Aluminum core in the middle
- Aluminum base on the bottom
The standard fiberglass is replaced with aluminum surrounded by a dielectric in the aluminum PCBs. It usually has a copper layer on the top, which is used to trace the circuit. The main advantages of using aluminum in PCBs are:
- Better mechanical stability: can withstand higher mechanical stresses; expand less on temperature changes, which result in a lower pealing risk
- Low cost: aluminum is a common element on earth, which is cheap to process and mine
- Excellent heat transfer: aluminum is one of the best heat dissipaters. It cools fast. Thus, localized high-power elements onboard is cooled more quickly without affecting neighboring components.
- Durable: aluminum is more durable than other materials like fiberglass and ceramics. Can withstand high mechanical loads and stresses.
- Lightweight: Aluminum is lightweight yet durable enough for mechanically critical applications.
- Environmentally Friendly: aluminum is non-toxic material which can be easily recycled
The critical applications to consider using aluminum-based boards are primarily associated with power electronics where a need to dissipate heat effectively is vital. Where ordinary cooling may not be sufficient or board space is limited. These might be:
- Power LED lighting applications – high-power LEDs dissipate vast amounts of heat, and there is a risk to overheating silicone dice. Aluminum-based boards effectively take this heat away.
- Power supply – power supply adapters can be tiny in size. For adequate cooling, aluminum-backed PCBs can help reduce the size and still carry high loads.
- Power electronics – including motor controllers, solid-state relays, high-frequency devices, and audio amplifiers.
If you are looking for effective heat control for your electronic device, aluminum boards are worth considering.
Copper PCBs
Copper PCBs have similar properties to aluminum, just with better performance. Copper has better thermal conductivity, so selecting PCBs with copper base should be considered where thermal management is critical. Copper material is more expensive, so aluminum is a more popular choice.
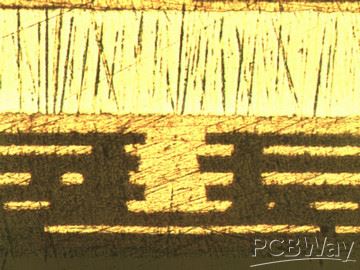
Copper-based PCBs may be selected for high-frequency circuits and precision circuits. Copper is more comfortable to process than aluminum.
Rogers PCBs
Rogers PCBs are somewhat similar to FR4 laminates. The only difference is that instead of regular fiberglass/epoxy, a PTFE (Teflon) material is used, which performs better in very high-frequency applications.

Teflon-based cores are less lossy at high frequencies and are the best choice in RF applications where more than 10GHz frequencies are used. However, Teflon boards have a high cost and have high heat resistance. A workaround is to use SiO2 and fiberglass fillings to reduce thermal resistivity. Teflon is harder to process and has lower adhesion to copper, so the manufacturing process is more complex and expensive.
Order Advanced PCB from PCBWay

Those PCB types can be manufactured at PCBWay, where you can choose many options, materials, and post-processing finishes. Currently, they are offering a 30% discount on advanced PCBs, so there is an excellent chance to take your design to a new level.