Automotive robots are simply robots used in the car manufacturing industry. These computer programmed machines are scheduled to perform a series of complex actions automatically. Automotive robots can either be autonomous or semiautonomous in nature.
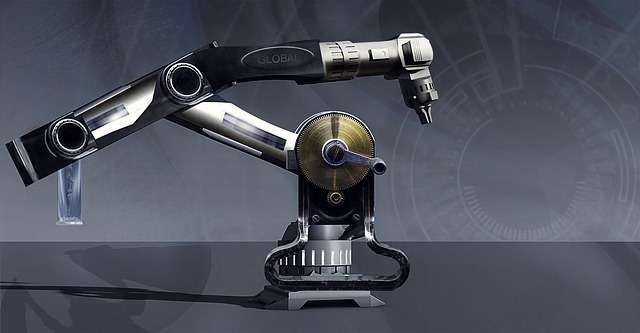
Applications done by Automotive Robots
Robots exist in different types with specific elements that make them best suited for different applications. Automotive robots are used to carry out some of the following applications:
- Welding
- Assembly
- Part transfer
- Material removing
- Machine tending
- Painting
Welding
Cars require a lot of welding before they are complete. Welding exposes workers to health risks since it involves high temperatures, thereby making automotive robots invaluable. Large robots will spot weld the car body panels, and the smaller robots will weld subassemblies, including mounts. Robotic welding ensures each fabrication is weld with the same high quality giving a well-finished product.
Assembly
Tasks like mounting wheels, screw driving, and windshield installation are suitable for robotic assembly. For instance, Delta machines, known for their high speed, assemble smaller components such as motors and pumps.
Part transfer
Some processes, such as pouring molten metal, are best done by automotive robots because of the danger they pose to human beings. The part transfer also includes transferring metal stamps from one press to another.
Material removing

This includes cutting and trimming tasks. For instance, cutting headliners or trimming flash from die castings and polishing mold. Automotive robots scheduled to perform material-removing have force-sensing technology that lets the robot maintain constant pressure against a surface.
Machine tending
These are processes such as unloading hot moldings from die casting machines or injection molding. Due to the danger posed by such processes, automotive robots are best suited.
Painting
Robotic painting reduces the health risks painting poses to human beings, thereby reducing risks. It also requires consistency and to be carried out quickly, making automotive robots ideal for the job.
Types of Automotive Robots
The common types of automotive robots are:
Cartesian
They consist of three joints and used the Cartesian coordinates system X, Y, and Z. They are easy to use and best-fit pick and place applications due to their linear movements of the cartesian elements. Their major drawback is the complexity of assembly required. Overall, their flexibility in configuration allows them to meet specific plant needs.
Cylindrical
Most are made of two moving elements: rotary and linear actuators. Their selling point is their space economy because they have a cylindrical work envelope and their installation and use are not complex. They have a rotation element making it possible to work anywhere around them.
Delta
They are the fastest because they have a unique, dome-shaped work envelope and are also the most expensive. They are best for pick-and-place or product transfer applications. They operate with great speed and precision.
SCARA
They are all-in-one robots, meaning they are equipped with x, y, z, and rotary motion. SCARA robots, even though similar to both Cartesian and Cylindrical robots they move quicker than the two. They have a smaller work area because they have a similar work envelope to Cylindrical robots.
6-Axis
6-Axis is another all-in-one robot that operates like a human arm. Therefore, it can pick and move materials from one plane to another. Although in terms of speed they compare to SCARAs, their programming is more complicated. They are the largest of the five robot types.
Choosing the Best Fit
When choosing the type of automotive robot, one must consider factors such as speed, orientation, load, precision, travel environment, and duty cycle. Determining these factors will ensure the corresponding robot will give the most effective and efficient results.
Conclusion
Clearly, there are many factors to consider when deciding what robot is best suited for every application. Plus, the use of automotive robots translates to higher customer satisfaction, lower health risks to human beings, and fewer mistakes.