PCB assembly is one of the most critical steps to ensure a working device. If your design is well made, all component is in place, assembly and soldering is a big step to working prototype. Unless you are a hobbyist or small startup, assembly is usually performed in a fab house, with the proper equipment and trained personnel. Modern electronics deals mainly with SMT parts that are getting smaller and smaller. A human can hardly manage manual work with such tiny components. Most of the job is done automatically with pick and place machines.

What is PCB assembly?
PCB assembly is a process from bare to finished working board with working components. The process takes several steps to accomplish:
- Preparing the board surface
- Placing parts
- Soldering
- Cleaning
- Testing
Each of these steps can also be divided into smaller steps. For instance, placing parts, which is a complex task, requires the preparation of components, placing reels and tapes for proper placing, setting the computer parameters. Larger or oddly shaped components may be required to place manually.
Other steps also take many actions to accomplish. Each of them requires special knowledge and experience.
The main advantages of inhouse assembly
In-house SMT assembly is advantageous in many ways. The manufacturer already has working equipment and the team set up for one purpose – making great PCBs. Without those, you will never achieve high-quality assembly, no matter how good you are at it. Engineers are working with different complex boards every day, so they are confident that you will get a quality product. Automatic processes reduce the risk of failure in many stages. Before manufacturing and assembly, engineers perform multiple design checks.
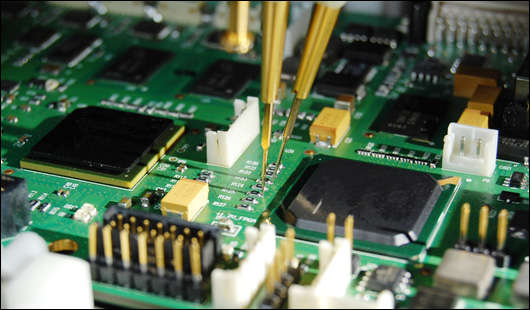
Equipment can work with the smallest SMT parts; sometimes, the human eye can barely see. Proper design and small components can ensure compact board sizes, better performance, and in many cases, less cost. Automatic assembly processes guarantee high reliability. Testing after assembly ensures that reliability is consistent. Assembly service also takes care of preparing necessary stencils for any SMT part. In most cases it is a free option.
The disadvantages of Turn Key Assembly services
There are not many disadvantages of using a Turnkey PCB assembly service. In the end, you always get high-quality PCB that passes quality control; components are sourced from reliable suppliers with the best pricing. We can mention a couple of disadvantages that may apply in special cases:
- You lack most of the control during the process. If you start the assembly process and spot an error in your design, you probably won’t make immediate tweaks.
- You have a little control of sourcing components if you choose turnkey supply. However, manufacturers have great sources, so you probably don’t need to worry about this. You always have an option to supply all or partial parts by yourself.
- If you need to manufacture a single working prototype and you have a handful of required components, you may save some cost by soldering by yourself. This way, you lose quality and. However, the costs of PCBA are so low; you can barely save anything, even time.
How SMT assembly is different from through-hole
SMT and through-hole assembly processes are different in placing and soldering. Automatic placement of through-hole components is a tricky task, as the leads of components should be fitted through tiny holes. Leads of each component may be bent a bit differently. This is why through-hole components usually are placed by hand, and thus it takes more labor time and thus is more expensive. On the other hand, SMT components are placed on the surface by a pick and place machine that uses a camera-based detection of pads and places components precisely.
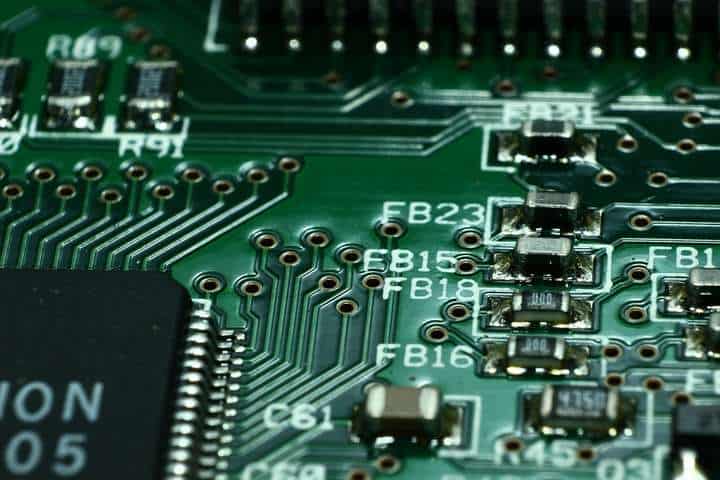
Soldering also is different. Through-hole components are soldered using the wave soldering technique, while SMTs are baked in a reflow oven where SMT solder paste melts and solders components. In reality, there are still many electronics where mixed components are used, so the assembly process involves both techniques. To keep the costs down, it is better to stick to SMT for all components, including connectors, headers, and other odd components.
Parts supply for assembly
The big advantage of in-house SMT assembly that you can leave parts to supply up to the manufacturer. This significantly reduces the time of manufacturing. For instance, PCBgogo can supply all the parts as they have contracts with many local suppliers to give the best prices. You don’t have to order and send components by yourself, which is a time-consuming process. There is also an option to supply all parts by yourself. If you have a specific need for some parts, you can also supply parts and leave the rest for the house.
PCBgogo is quite flexible. They can assemble individual boards or panelized them. The assembly can be on one or both sides of the boards. The components may be through-hole or SMT. Additionally, you may select functional testing and firmware loading to devices. The final assembly may be coated and even X-ray tested to ensure proper solder adhesion under SMT parts. You may also get BGA assembly, Rigid-Flex assembly, or mixed PCBA. Check out their PCBA quote form for more details.
When you start ordering PCBA service, you need to supply a PCB file. If you order a PCB prototyping service, this part is already done. PCBgogo accepts multiple file formats, including Gerber, PCBDOC, Eagle, and many more. Be sure to contact support if unsure.
Also, it is essential to supply a Bill Of Materials (BOM). Usually, when designing a circuit, you select components that are listed automatically. You can additionally include supplier part numbers like DigiKey, or Mouser.
Provide any other information that would help setting Pick & Place machine. These include a surface legend, center coordinates of the part, correct part numbers, component rotation angles, possible 3D files. The more useful information you will provide, the better and faster results you will get.