Plastic injection molding is an extremely versatile method of producing plastic parts and has multiple advantages over other methods of rapid prototyping. The process is more straightforward and more reliable than in many different ways. The benefits of this process are as follows:
1. High Efficiency- Fast Production
The process is quite fast compared to other methods, and the high output rate makes it even more efficient and cost-effective. With the short run cycles, a higher number of moulds can be produced in a limited amount of time, thus increasing revenue and profit margins. Typically, hot-runner ejection mould systems provide parts with more consistent quality and do so with faster cycle times. Also, the plastic injection moulding process takes little time, and this allows more parts to be manufactured from a single mould.
2. Complex Part Design
Injection moulding can handle remarkably complex parts, and uniformity, as well as the ability to make millions of virtually identical pieces. Key design elements should be taken into account when maximising the precision and quality of your parts. With the right design, parts can be made quickly and with quality. There are essential design elements that should occur during the injection process for the work to complete correctly. They include the thickness of the wall, designed rib, boss design and transitions in the corner. Furthermore, complex and intricate shapes can efficiently be developed due to the high pressure that is given during the moulding process.
Plastic injection molding is an extremely versatile method of producing plastic parts and has multiple advantages over other methods of rapid prototyping. The process is simpler and more reliable than many other methods .The advantages of this process are as follows:
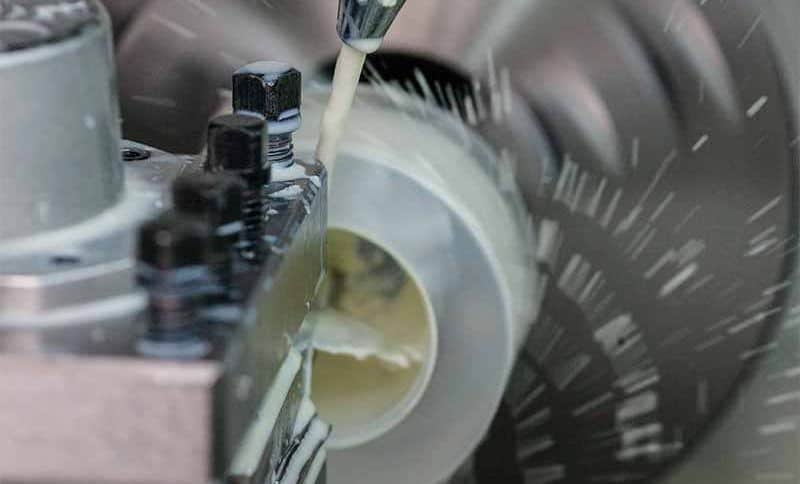
3. Enhanced Strength
Strength is one of the key factors that needs to be determined when designing a plastic injection molded part. Material selection plays another key role in the strength of the part.
4. Flexibility- Material and Color
Choosing the right material and color for a project are two of the essential factors in creating plastic parts. Due to the wide variety of both, the possibilities are almost endless. It is important to work with an injection molder that has experience with a variety of resins and applications, including resins that are compliant with FDA, ROHS. Plastics can be colored using various coloring systems, each of which offers its own unique properties, benefits, and drawbacks. Masterbatches,”salt and pepper” blends, Liquid Color, and precolored resins are four of the most common coloring techniques.
5. Reduced Waste
When looking for a high-volume injection molding partner, it’s important to consider companies’ green manufacturing initiatives. During the molding process, excess plastic is generated. You will always look for a company that has a system to recycle its waste and reduce any sort of pollution.
6. Low Labor Costs
7. Ability to Use Multiple Plastic Types Simultaneously
One of the most significant advantages of using plastic injection molding for manufacturing various part is the ability to use different types and qualities of plastic simultaneously. This can be done with the help of injection molding, which takes away the tension of using any particular type of plastic.
Using injection molding also ensures the parts manufactured hardly require any work after the production. This is because the parts have more or less a finished appearance after they are ejected from the injection molds.
Today, plastic injection molding is an environment-friendly process. The scrap plastic generated during the production process can be reused. Hence, the process generates very little waste, which can be considered negligible.