The physical distribution of goods from manufacturing plants to consumers account for a significant percentage of the product cost. Companies are now forced to adopt economical and efficient material-handling equipment. Among the various types of material handling equipment, conveyor systems have gained massive popularity due to their versatility. Conveyor systems can be used in many applications with success, keeping products moving at all times. They are essential to automate the manufacturing facility, and improve distribution and processing solutions. There are many aspects to take into consideration when selecting a system of this kind. Continue reading to find out what you need to review.
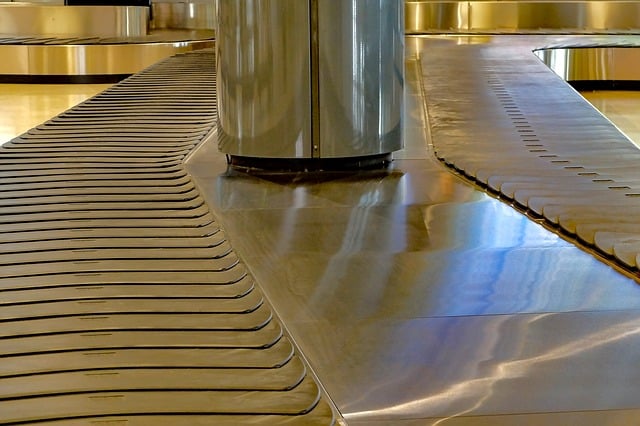
Type of material handling technologies
As far as handling products is concerned, you have two main types of mechanical devices to choose from. The difference between them isn’t so significant. All conveyor systems consist of frames, and they support bulk materials. Anyway, these are the main types of material handling technologies:
- Manual Conveyors – as the name clearly suggests, the mechanical device is operated manually. It needs human input to convey the products through the finishing line. Not only are they cost-effective, but they will help you save up on floor space.
- Automated conveyor systems – The materials are automatically loaded and controlled. Efficiency in the production line is guaranteed. The great thing about automated systems is that they can be equipped to fit individual needs. Custom industrial conveyor systems do the job better than standard material handling technologies.
Product specifications
Acquiring a conveyor system requires careful planning and execution. What you need to do is to find a solution that improves the bottom line results. In this sense, taking into account product specifications is essential. The dimensions of the product, such as length, width, and height, determine the choice of the mechanical device. The weight of the product is just as important. Why? Because the weight has a tremendous impact on motor sizing. You can’t just haul 100 kg onto a plastic conveyor. It may not be able to withstand the weight. Last but not least, you can’t afford to ignore product type. Let’s say that you’re handling wooden pallets. The best solution in your case is a CDLR. This device is capable of handling bulk items with smooth bottoms. Don’t judge a book by its cover. Look more closely. You get the point.
Better conveyor system maintenance
The last thing that you want is to end up with technology that is difficult to maintain. Your goal is to decrease spending, not increase it. You’re running a production facility, and any kind of disruption costs you money. Things should go as smoothly as possible. Look for a conveyor system that doesn’t let you down when you need it the most, and that is easy to take care of. Costly system breakdowns should be the least of your worries. What you should worry about is how to improve the customer experience. Get yourself a powerful tool that doesn’t require too much maintenance. It’s possible to find such a mechanical device.